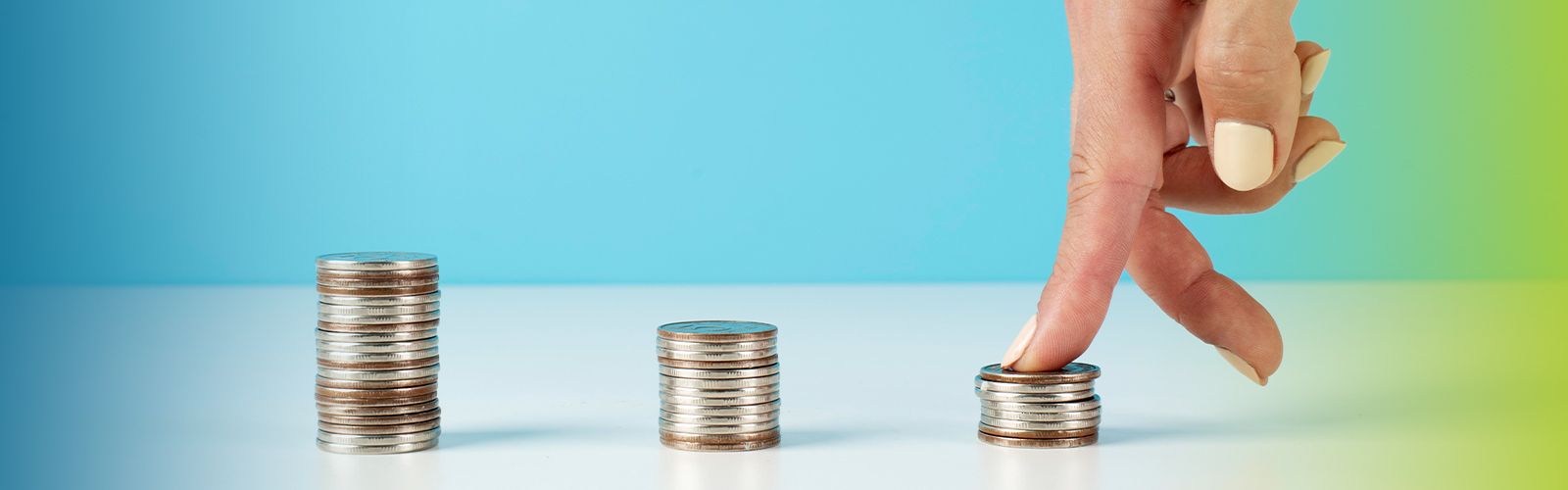
Reducing Operating Costs in Dedusting Systems
Dedusting systems take a very significant share of the general production costs of enterprises with the electrical energy they use for their fans, their compressed air consumption and their consumable filtration elements.
An inefficient dust collection unit not only threatens employee health, but also causes both loss of reusable product and wasted costs.
The most common causes of inefficiency are;
- Faulty collection ducts,
- Incorrect fan selection,
- Insufficient shaking air,
- Incorrect filter element selection
Asel Endüstriyel tries to use advanced engineering techniques to prevent these errors that may cause loss of efficiency in the dedusting systems it has established with 20 years of industrial industry experience.
Engineers within Asel Industrial design each dust collection system specifically for the customer.
First of all, solid modeling is done for dust collection ducts. Then these ducts are run virtually with fluid simulation software. The duct project is completed with the pressure loss from the system and flow data corresponding to the optimum velocity.
Thus, the duct diameters, duct form and ventilator selection are chosen correctly in terms of both efficiency and energy efficiency.
The most common mistakes in dust collection systems are narrow ducts causing excessive resistance or too wide ducts causing dust settling.
Cleaning/shaking the right filter element with the right air
Again, one of the factors that reduce the efficiency of dust collection units the most is the selection of the wrong filter element.
In the process,
- Dust load
- Grain distribution of the powder,
- Dust stickiness,
- Powder abrasiveness,
- Nem,
- Temperature
It is very critical to study such factors correctly and select the appropriate filter element.
An incorrectly selected filter element will not allow you to work efficiently even if everything else is in order.
Another critical issue is the cleaning/shaking air.
- At the appropriate pressure,
- Appropriate flow rate,
- Appropriate quality
The use of purge air is very important.
The most common mistake is that the diameter of the air line brought to the unit is smaller than it should be and air is supplied at a much lower pressure than that produced in the compressed air center.
Another issue is the condensation that occurs in long and uninsulated air lines and the problems caused by cleaning with wet air.
The most important points to be considered for an effective dust collection system with minimum operating costs are briefly explained in this article.
Written by: Dr. Barkın MİNEZ (Mechanical Engineer)